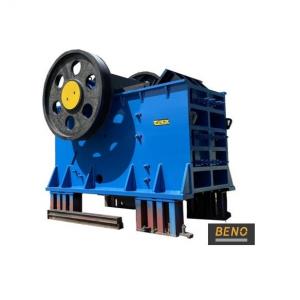
Add to Cart
295-350 TPH Output Jaw Rock Crusher Jaw Crusher For Primary Crushing
Equipment introduction
A jaw rock crusher, also known as a toggle crusher, is a machine used for primary crushing of various materials in the mining, construction, and aggregate industries. It is one of the most commonly used crushers due to its simplicity and versatility.The jaw rock crusher consists of a fixed jaw plate and a movable jaw plate. The fixed jaw is vertically fixed on the front wall of the machine frame, while the movable jaw is positioned in a V-shaped alignment. The movable jaw reciprocates, or moves back and forth, against the fixed jaw, crushing the material in the process. Jaw rock crushers are designed to exert a force on the material, breaking it into smaller pieces. The crushing action is achieved by the vertical movement of the movable jaw, which applies pressure to the rock and forces it against the fixed jaw. This process results in the fragmentation of the material into smaller, more manageable sizes.
One of the key advantages of a jaw rock crusher is its ability to handle a wide range of feed sizes. The large feed opening allows for larger-sized rocks and materials to be easily fed into the crushing chamber. Additionally, the adjustable discharge setting enables control over the final product size. Another notable feature of jaw rock rock crushers is their high efficiency and low operating costs. The mechanical advantage provided by the large mechanical advantage provided by the two jaw plates allows for efficient crushing with minimal energy consumption. This makes jaw rock crushers suitable for both primary and secondary crushing applications.
A jaw rock crusher is a versatile and efficient machine used for primary crushing in various industries. Its simplicity, wide feed opening, and adjustable discharge setting make it a popular choice for processing different types of materials. Whether it's mining, construction, or aggregates, jaw crushers play a crucial role in breaking down rocks and materials into smaller sizes.
Equipment parameters
Model | XCE1012 |
Feed port size | 1000*1200mm |
Maximum feeding side length | 850mm |
Adjustment range of outlet | 105-175mm |
Production capacity | 295-350t/h |
Power | 160 |
Speed | 200 |
Weight | 52 |
Equipment trait
Jaw rock crushers possess several characteristics that make them widely used in various industries. Here are some key features of jaw rock crushers:
High Crushing Ratio: Jaw rock crushers are designed to have a high crushing ratio, which means that the size of the feed material is reduced significantly in a single pass. This enables efficient and effective crushing of large rocks and hard materials.
Simple Structure: Jaw rock crushers have a simple and robust structure, consisting of two main components - the fixed jaw plate and the movable jaw plate. This simplicity makes maintenance and repair relatively easy, reducing downtime and ensuring smooth operation.
Adjustable Discharge Setting: Jaw crushers allow for the adjustment of the discharge setting, which controls the size of the final product. This feature enables the production of various product sizes to meet specific requirements.
Wide Feed Opening: Jaw rock crushers have a wide feed opening, which allows for the processing of large-sized materials. This makes them suitable for primary crushing applications in mining and quarrying industries.
Working principle
The working principle of the jaw rock crusher is based on two main components: the fixed jaw and the movable jaw. The following is a brief description of the working principle of the jaw crusher:
Starting position: In the initial state of the jaw rock crusher, the fixed jaw plate is fixed on the front wall of the crusher, while the movable jaw plate is connected to the fixed jaw plate in a V shape.
Movement process: When the crusher starts to work, the movable jaw moves up and down driven by the eccentric shaft. This movement transfers pressure to the material and presses it against the fixed jaw.
Crushed material: When the movable jaw moves downward, the material is pressed against the fixed jaw, and then crushed by pressure and shearing force. During this process, the material gradually becomes smaller and is discharged through the outlet of the crushing chamber.
Repeated cycle: The movable jaw plate continues to move up and down, repeating the process of crushing materials until the required particle size reaches the requirement.
It should be noted that the crushing cavity of the jaw crusher is also equipped with some adjustable devices for controlling the size of the discharge port. In this way, the discharge size of the jaw crusher can be adjusted as needed to meet specific crushing requirements.
In short, the jaw rock crusher crushes and decomposes the material into smaller particles through the up and down movement of the movable jaw. This crushing process is accomplished by the pressure and shear force between the fixed jaw and the movable jaw.